Porosity in Welding: Identifying Common Issues and Implementing Ideal Practices for Avoidance
Porosity in welding is a pervasive concern that frequently goes unnoticed until it creates substantial issues with the integrity of welds. This usual flaw can compromise the toughness and longevity of bonded structures, posing safety and security dangers and resulting in costly rework. By recognizing the root causes of porosity and carrying out efficient prevention approaches, welders can substantially improve the top quality and dependability of their welds. In this discussion, we will certainly explore the vital aspects contributing to porosity development, analyze its harmful results on weld performance, and review the very best practices that can be embraced to minimize porosity incident in welding processes.
Common Sources Of Porosity
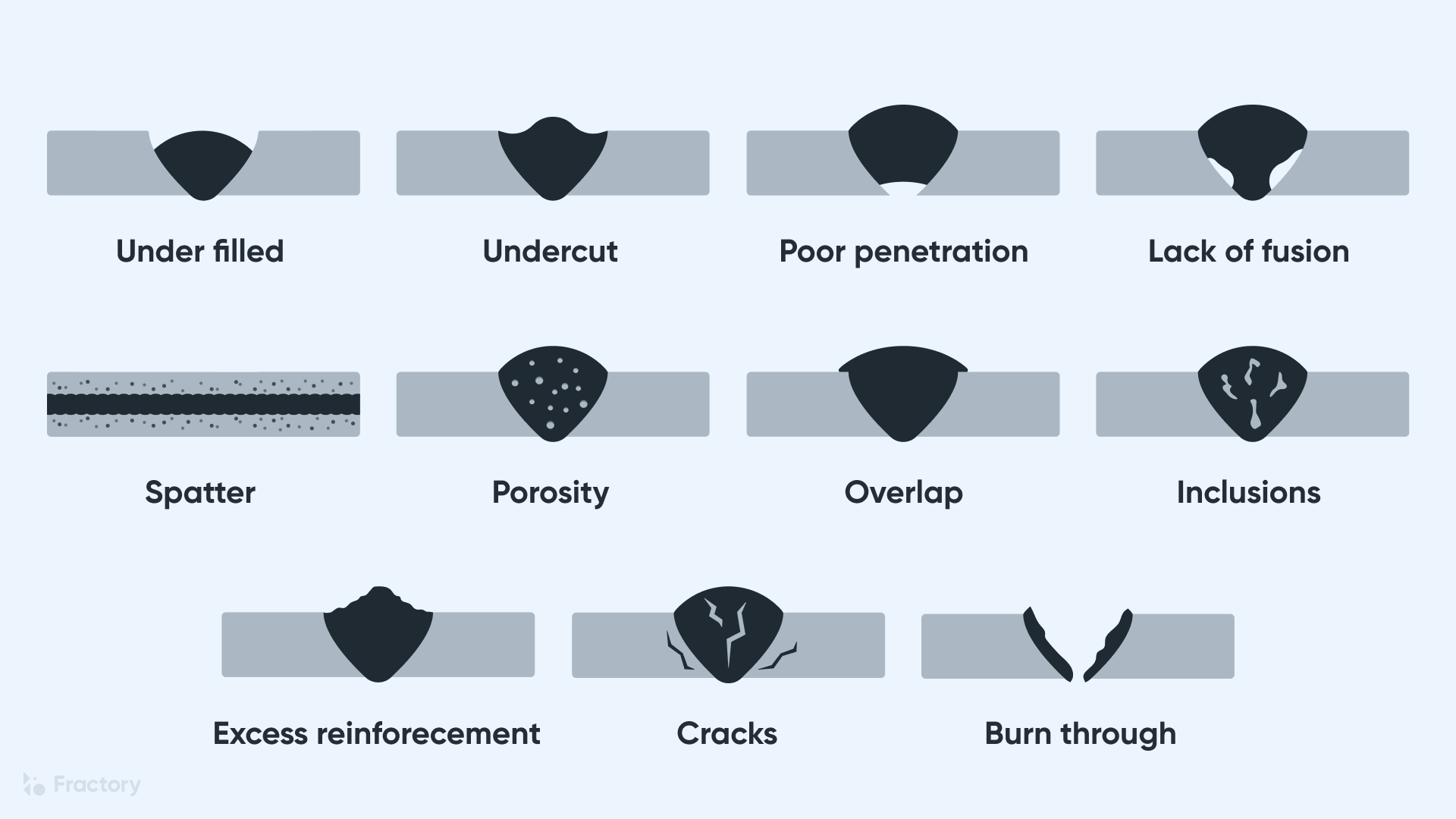
Utilizing dirty or damp filler products can introduce impurities right into the weld, contributing to porosity issues. To minimize these usual causes of porosity, comprehensive cleansing of base steels, correct protecting gas selection, and adherence to optimum welding specifications are vital practices in attaining top notch, porosity-free welds.
Effect of Porosity on Weld Quality

The visibility of porosity in welding can considerably endanger the architectural integrity and mechanical buildings of bonded joints. Porosity creates voids within the weld metal, deteriorating its total strength and load-bearing capacity.
Among the key effects of porosity is a decrease in the weld's ductility and strength. Welds with high porosity degrees often tend to show lower impact stamina and minimized capability to flaw plastically prior to fracturing. This can be specifically worrying in applications where the bonded parts are subjected to dynamic or cyclic loading conditions. Porosity can restrain the weld's capacity to successfully send pressures, leading to early weld failure and potential safety hazards in crucial structures. What is Porosity.
Ideal Practices for Porosity Avoidance
To improve the structural honesty and high quality of welded joints, what details actions can be carried out to reduce the occurrence of porosity throughout the welding process? Porosity avoidance in welding is vital to make sure the integrity and toughness of the final visit homepage weld. One effective method appertains cleansing of the base metal, eliminating any impurities such as rust, oil, paint, or moisture that might cause gas entrapment. Making certain that the welding devices is in great problem, with clean consumables and ideal gas circulation rates, can likewise considerably lower porosity. Furthermore, keeping a stable arc and regulating the welding parameters, such as voltage, existing, and travel speed, aids create a regular weld pool that decreases the risk of gas entrapment. Utilizing the correct welding method for the details material being welded, such as readjusting the welding angle and gun setting, can better avoid porosity. Routine assessment of welds and immediate remediation of any kind of issues determined throughout the welding procedure are important methods to stop porosity and produce top notch welds.
Importance of Appropriate Welding Methods
Implementing correct welding methods is paramount in ensuring the architectural stability and quality of bonded joints, building upon the structure of effective porosity avoidance measures. Too much warm can lead to increased porosity due to the entrapment of gases in the weld swimming pool. Additionally, utilizing the appropriate welding specifications, such as voltage, existing, and travel rate, is essential for attaining sound welds with very little porosity.
Furthermore, the option of welding procedure, whether it be MIG, TIG, or stick welding, must line up with the specific needs of the project to index make sure optimal results. Appropriate cleansing and preparation of the base metal, along with selecting the best filler hop over to these guys product, are also vital elements of efficient welding strategies. By sticking to these ideal practices, welders can decrease the danger of porosity formation and produce top quality, structurally sound welds.
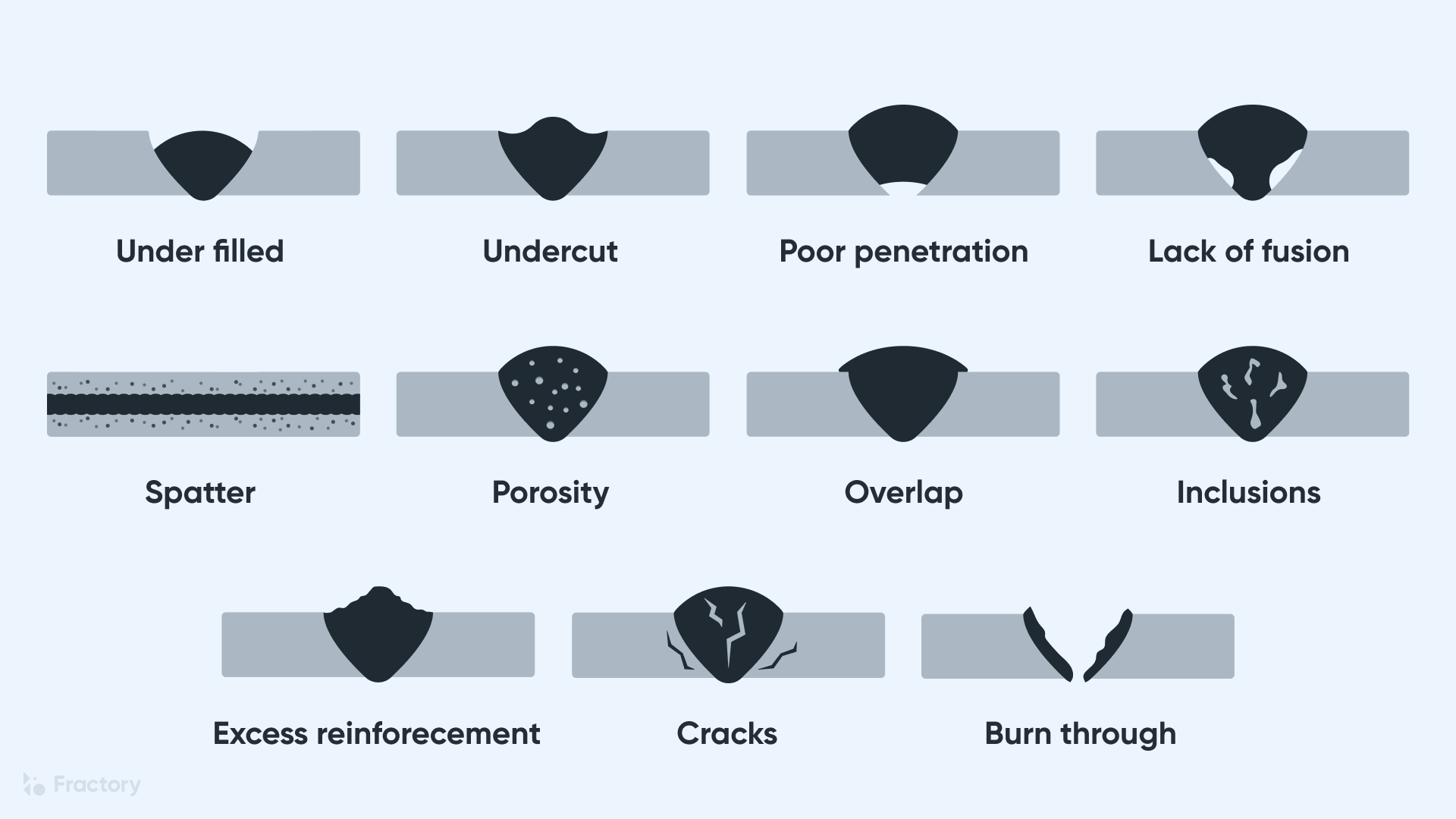
Evaluating and Top Quality Control Measures
Evaluating procedures are crucial to identify and protect against porosity in welding, ensuring the toughness and durability of the last item. Non-destructive screening techniques such as ultrasonic testing, radiographic testing, and visual examination are generally used to determine prospective problems like porosity.
Conducting pre-weld and post-weld examinations is likewise crucial in keeping quality assurance standards. Pre-weld examinations include verifying the products, equipment setups, and cleanliness of the job area to avoid contamination. Post-weld inspections, on the various other hand, assess the last weld for any issues, including porosity, and validate that it meets defined standards. Carrying out an extensive quality assurance plan that consists of thorough screening procedures and assessments is paramount to minimizing porosity issues and making sure the total quality of bonded joints.
Final Thought
To conclude, porosity in welding can be a common issue that impacts the high quality of welds. By determining the usual sources of porosity and applying best practices for prevention, such as proper welding strategies and testing measures, welders can make certain top quality and trusted welds. It is important to prioritize avoidance techniques to minimize the event of porosity and maintain the honesty of welded frameworks.